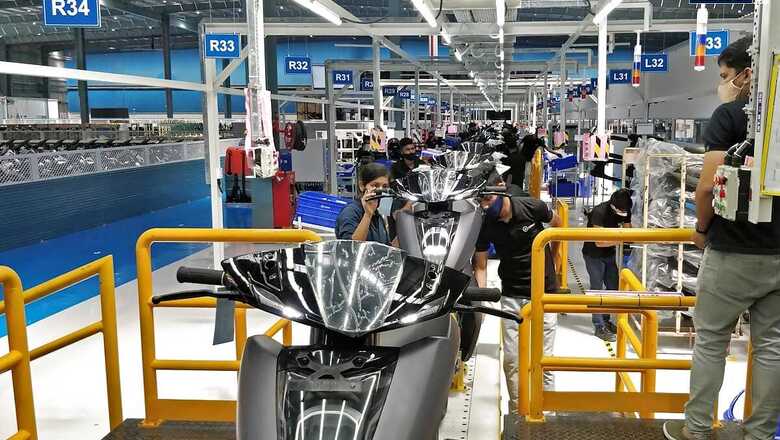
views
If you haven’t heard it yet, the new buzzword in town is electric. Now while automakers in the four-wheeler segment are pouring millions of dollars to have a few EVs in the portfolio, the story in the two-wheeler segment is different as not a lot of established brands have dipped their toe. However, among the top of the ones which have, in India, is Ather Energy. Today we are here at its recently-inaugurated facility in Hosur to give you a glimpse about how an electric scooter is manufactured from scratch to the point where you take it home. So without further delay, let’s get into it.
Also Watch:
Now, a lot of you might not know this, but back when Ather Energy became a reality, the two founders of the company had planned to manufacture just the batteries for other automakers in India. Soon, the goal changed and instead of the batteries, Ather started its journey with the 340 and the 450 electric scooters. A while back, citing low demand, the company had to discontinue the 340, but the 450 continued having two variants on offer. The company now sells the advanced versions of the 450 as the 450 Plus and the 450X. Currently operating in 15 states across the country, Ather plans to expand its footprint and along with it, ramp up its production. Hence, the new facility at Hosur.
Ather’s new facility at Hosur spreads across an area of 1,23,000 sq ft with an annual capacity of 1.10 lakh electric scooters and 1.20 lakh lithium-ion battery packs. In a very likely scenario where the company sees substantially rising demand in the future, the plant is scalable by three times. Just by tipping over an adjoining wall the facility will up the number to around 4 to 5 lakh units. The production of Ather 450X and 450 Plus electric scooters takes place on a 37-station assembly line that is manned by around 70 workers.
The process of assembly begins with the basic skeleton which is made by joining its aluminium-chassis and rear sub-frame. Post this the in-house developed battery is bolted on the scooter. Following this, the scooter gets components like its wheels, suspensions before it is forwarded to et the electricals such as the instrument cluster, lights and more. Post the final station that scooter is put up for a quality check where it is put on the dyno to test its acceleration, braking, top-reverse mode and other performance aspects.
Finally, before the scooter is passed for delivery, it goes through a 1-km real-world test. Another interesting aspect of Ather’s new plant is that it generates zero effluents, which helps in reducing the environmental impact of running a production facility; all e-wastes are being handled by authorised recyclers. The new facility has been set up with an investment of Rs 130 crore and the company will be investing Rs 635 crore over the next five years. With the new factory, Ather says that it has ramped up its production capacity by almost 10 times.
So, as the Luddites could not stop the technological revolution, no one can stop this major shift. In a few coming years, a lot more established manufacturers will be seen shifting to a production type like the one at Ather. Hence, it does not need to be said, that if this is the future, it’s not so dull.
Read all the Latest News, Breaking News and Coronavirus News here
Comments
0 comment