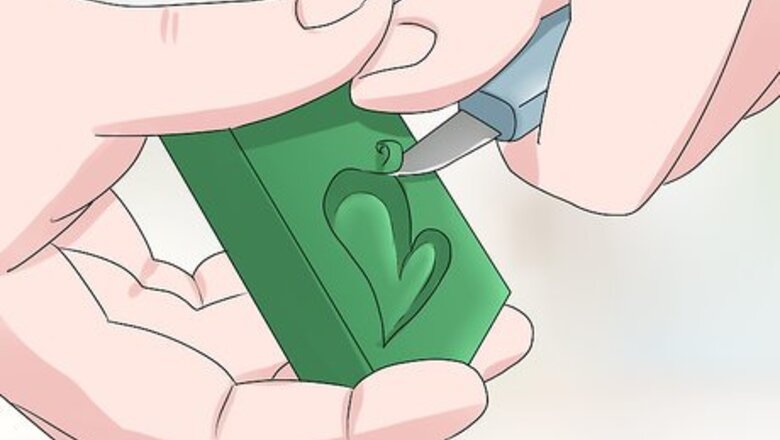
views
Crafting Your Mold
Carve a piece of hard modeling wax into your desired shape. Start simple for now, as complex molds are much harder to keep together at first. Get a piece of modeling wax and use a precision knife, Dremel, and any other tool needed to make a model of your jewelry. Whatever shape you make now will be the shape of your finished piece. You are making an exact replica of your eventual jewelry. Using a piece of jewelry you like as a model will help you design better pieces when you first start.
Attach 3-4 "sprues," wax wires that will provide a channel for the wax to melt out later. Using some more wax, craft several long, wires out of wax and attach them to the model so that they all lead away from the piece. This is easier to understand when you see the whole process—this wax will be covered in plaster, then melted out to make a hollow version of your shape. You then fill in the hollow part with silver. f you don't make sprues, the melted wax can't actually get out and make a hollow area. For smaller pieces, like a ring, you may only need one sprue. Larger pieces, like belt buckles, may need up to ten. All the sprues should meet at the same place. They will need to be attached to a sprue base.
Attach the mold to the sprue base using a bit of melted rubber. The sprues all meet together, and you attach the mold to the sprue base where all the sprues meet. This allows the wax to melt through the bottom of the base and leave the mold.
Put the flask on top of the sprue base, making sure you have a quarter inch between the wall of the flask and the model. The flask is a big cylinder that slides on top of the sprue base.
Investing the Mold
Secure the wax model stand to the bottom of a casting flask, using more melted wax. The model should be propped up in the flask. It is ready for the jewelry casting process. Note: In the video, the excess silver parts are other pieces of jewelry going along with the belt buckle. They are not extra sprues or necessary additions.
Mix the dry ingredients of the gypsum plaster-based investment mold material with water, as per manufacturer's directions. Follow the instructions of whatever investment mold you choose to purchase—it should be a simple set of measurements. Wear a mask or respirator whenever possible as you work with this powder—it is not safe to inhale. Move on once you have the mix the consistency of pancake batter.
Place the investment mold in a vacuum chamber to remove any air bubbles. If you do not have a vacuum sealer, you can just let it sit for 10–20 minutes. Air bubbles will create holes, which may allow the metal to seep in and create a pock-marked final piece of jewelry.
Pour the investment mold mixture into the flask, surrounding the wax model. You will completely encase your mold in plaster. Re-vacuum the mixture to get rid of any last, small bubbles before moving on. Wrap a layer of tap around the top of the flask, so that half the tape sit's over the lip and helps contain the plaster from bubbling over.
Allow the investment mold to set. Follow the exact instructions and drying time for your plaster mix before moving on. When done, remove the tape and scrape any excess plaster from the top of the mold.
Place the entire flask in a kiln set to approximately 1300 degrees F (600 degrees C). Note, different plasters may have different temperatures. However, you should not be at anything less than 1100. This will harden the mold and melt the wax away, leaving a hollow chamber in the center of the cast jewelry mold. This may take up to 12 hours. If you have an electronic kiln, try to set it to slowly raise the temperature up to 1300. This can help prevent cracking.
Remove the flask from the kiln while hot, and check the bottom of the mold for obstructions. Make sure that the hot wax can easily leak out of the mold, and that there is nothing obstructing it. If there is nothing in the way, shake the flask gently to make sure all the wax came out. There should be a puddle of wax in the reservoir of the flask or at the bottom of the kiln. Make sure you wear safety gloves and goggles.
Casting the Jewelry
Place your metal of choice in a pouring crucible, then melt it inside a foundry. The melting temperature and time will be determined by the type of metal you are using. You can also use a blow-torch and small crucible to melt your silver.
Use a jeweler's centrifuge (Centrifugal Casting Machine) to pour the metal into the mold. For professional jewelry, you'll need a centrifuge. This evenly distributes the metal quickly, but it is not the only option you have for casting. The more classic, easier solution is to simply pour the metal careful into the tunnel left by the base of the mold. You could use a large, metal-specific syringe to pump the metal into the mold, too.
Allow the metal to cool for 5–10 minutes, then dunk it slowly in cold water. The amount of time it needs to cool is dependent, of course, on the metal melted and used. Dunk too soon and the metal may crack—dunk too late and it will be hard to remove all the plaster from the hardened metal. Look up cooling times for your metal before moving on. That said, if you're in a pickle you can just wait 10 minutes and then dunk in cold water. The plaster should begin dissolving away as you shake it around the cold water.
Tap the mold gently with a hammer to break away any excess plaster and reveal the jewelry. Separate the flask from the sprue base and use your fingers or a toothbrush to peel away any last bit's stuck to the jewelry.
Finishing Your Jewelry
Use an angle grinder with a cut-off wheel to cut away any lines of metal from the sprues. Cut away the thin pieces of metal that you needed to create a hole to pour the metal in. A hand-held grinder should be more than strong enough.
Consider and acid bath or wash to clean off any last bit's of plaster. The firing process often leaves metal dingy and dirty looking. You can look into specific washes for certain metals, which will lead to a much nicer shine and an easier job cleaning up the piece later.
Buff out any irregularities on the jewelry piece using a metal buffing wheel. Use files, enamel clothes, polishes, etc. to clean the piece up to your desired style. If you planned on setting a stone, do it after you finish polishing.
Comments
0 comment