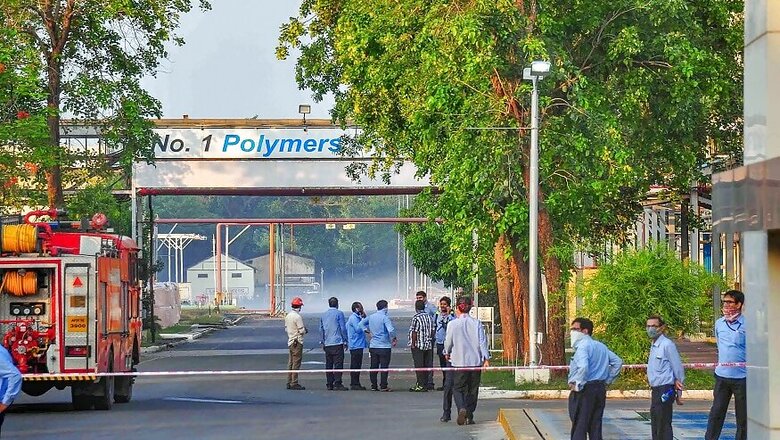
views
A Chain of industrial disasters
After 20 April, industries in India have been allowed to operate outside contained zones for the first time since the augmentation of lockdown 24 March. A huge number of factories in green and orange zone which hastily wrapped up within a short notice of a few hours began preparing to restart production. But, around this time only, a series of industrial accidents shook the country. A major gas leak happened in a plant near Visakhapatnam in LG Polymers chemical plant causing the death of at least 12 people and numerous cattle. One similar gas leak (in a paper mill in Raigarh, Chhattisgarh) and one boiler blast (Neyveli, Tamilnadu) followed. While these events were being investigated, on 22 May, Pune in Maharashtra saw a major fire break out in a chemical factory.
These series of industrial accidents raised some questions. While industrial activities will restart slowly and gradually, we need to understand why these unfortunate events keep happening? Does the lockdown have any relationship with these occurrences? And how they can be stopped from recurring in future?
What caused the accidents?
The gas that has been identified as the primary suspect for the Visakhapatnam gas leak is Styrene, a neurotoxin. On the wake of the lock down, the plant was hastily shut down with a large bulk of chemical stored in the tanker. The long stagnancy of next six weeks made way for some chemical changes inside the storages causing auto-polymerisation. Auto-polymerisation is a chemical reaction that can happen when Styrene is stored for a long time in liquid form in stagnancy, which in this case it was.
In the Raigarh case, poisonous gas accumulated in the recycling chamber of a paper mill during the six weeks of lockdown causing the hospitalisaton of maintenance workers. The boiler blast in Neyveli Lignite Corporation India happened when the unit accumulated extra pressure which the employees were unable to bring under control. It ignited a cache of oil kept nearby and caused a flash fire that resulted in eight workers being hospitalised.
The Pune incident happened when a chemical manufacturing unit located in Kurkumbh MIDC on Pune-Solapur Road near Pune had burst into flames. The fire started from drums containing acetone and ethanol stored at the plant. No casualty was reported in the incident as the plant was closed.
Did lockdown play a role?
All these incidents happened in different places. But, there is a pattern. Three among the four cases happened in chemical industrial units. The Visakhapatnam plant was hastily shut down with a large bulk of chemical (the 2000 ton tanker that leaked had 1800 tons of Styrene) stored in the tanker. For the next six weeks, that chemical would rest. This long stagnancy made way for some chemical changes inside the storages. The valve in the unit had burst open due to auto-polymerisation. Auto-polymerisation is a chemical reaction that can happen when Styrene is stored for a long time in liquid form in stagnancy, which in this case it was. The mandatory temperature check was absent according to the information that is presently available to us. This check was required to keep the temperature of the tank below 17 degree to stop the material from vapourising. The number of staff present for maintenance in the plant on that fateful day also seems to be less than the minimum required.
The Neyveli Lignite Plant was working with a lower capacity in the lockdown with a skeleton crew. It was just staring to increase power generation when this incident happened. The plant was using a huge percentage of contractual workers instead of regular employees.
In the other two chemical plant accidents, long storage of hazardous chemicals might have created a favourable situation for some reactions that resulted in the release of poisonous gases or fire. As evident from the incidents, chemical industries are the most vulnerable in this situation. Huge amount of hazardous chemicals left undisturbed for long periods can lead to some unprecedented chemical reactions. The situation can become worse taking into account the grey practices regarding industrial safety.
Industrial safety in India and ground reality
Regarding industrial safety, India can boast of having one of the best standards and protocols. But, in reality, they are sometimes bypassed one way or the other. To begin with, the polymer plant in Visakhapatnam and the chemical plant in Pune used chemicals like styrene and acetone that fall under the scheduled hazardous chemicals in India. Both federal and state clearances are needed to handle them. This especially becomes important when the plant authority decides to expand the facilities. In the case of LG Polymers chemical plant, they did in fact expand. But, with state permit for starting a new business instead of actual federal clearances.
The fine lines of the amended ‘Factory Act’ permits use of hazardous technology if they give an undertaking that “The article will be without risks to the health of the workers when properly used.” Then there is the controversial issue of corruption and certification by inspectors without knowing the technicalities. These often leads to a number of institutions operating in a grey area regarding safety protocols. Well-trained safety personnel not being assigned is a serious problem. The Factory Act mentions the state government may assign a scientist having specialised knowledge of the hazardous process which will be involved in the site appraisal committee of the factory. But, this is left as an option and not mandatory.
According to the March 2017 notification of Indian Govt. industrial projects can legitimise construction, expansion and modernisation already under construction without prior environment clearance. The mechanism, supposed to be a onetime chance has become a fait accompli in last three years. Thirty one meetings have been held by the expert panel of Ministry of Environment, Forest and Climate Change to provide clearance for hundreds of similar projects. This definitely by passes the 2006 Environmental Impacts Assessment (EIA) rules. The new EIA 2020 document that is being drafted goes even further. It proposes to institutionalise this practice as long as the project developer reports the violation himself in front of an appraisal committee.
Cost cutting to maximize profit can be a dangerous decision when hazardous materials are involved. The Bhopal Gas Tragedy, one of the worst industrial disasters in Indian history, was a result of the same. In the case of Bhopal, water seeped into a storage tank of toxic liquid Methyl Isocyanate (MIC) that was stored in excess amount in Union Carbide India Limited’s pesticide plant. The water along with the rust from the old pipes caused a runaway exothermic reaction. The liquid material turned into overheated gas and escaped causing a huge loss of life.
In some old plants, rusty machinery and corroded pipes are still used for a long time without proper maintenance under the radar. The tendency of bypassing the regulations for convenience has been there in various degrees. The lockdown didn’t create that. It just highlighted the cracks in the system.
Steps forward in industrial policy
India is entering a harsh time. The COVID 19 crisis is threatening the whole world with the biggest depression since 1930s. The industrial institutions are trying to strategies a route for survival in the future economic fallout. But, while trying to maintain a profit margin, the safety and security of employees and the people living in the proximity of the industries cannot be compromised.
What India needs, is a full check on the clearances of hazardous industries to make sure they have both federal and state clearance for their activities. A scrutiny of the type and amount of chemicals being stored can be helpful to understand if any industrial unit is over their capacities in regard of storing hazardous chemicals. Strict implementation of protocols of Health Safety Environment and Quality Assurance should be given highest attention.
An official document pointing out towards the dangers of opening an industrial unit after lockdown or storing different types of hazardous chemicals, precautions taken by the employees, importance of using experienced and minimum number of employees can be helpful. The practice of tracking and reporting near missed Incidents should also be there. In its absence, the pattern of possibilities and risks regarding industrial accidents is incomplete. So should be the data about the hazardous materials used in Indian industries, their side effects and how they react in the long stagnation (like in the lockdown). Thus, India might be able to identify the industrial risks in the present scenario and take required actions to avert further industrial tragedies.
In the present situation, it has become extremely important to check the grey practices of Indian industry those were previously overlooked as ‘little compromises’. After all, no amount of ease of doing business is more valuable than human life.
The article first appeared in ORF.
Comments
0 comment